Understanding Welding WPS Specifications: Best Practices and Techniques for Quality Welds
In the world of welding, mastering Welding Procedure Requirements (WPS) standards is an essential element that straight affects the quality and honesty of welds. As we navigate via the ins and outs of welding WPS standards, discovering vital insights and strategies for attaining top-tier welds will be vital for welders looking for to excel in their craft and create welds that stand the examination of time.
Recognizing Welding WPS Standards
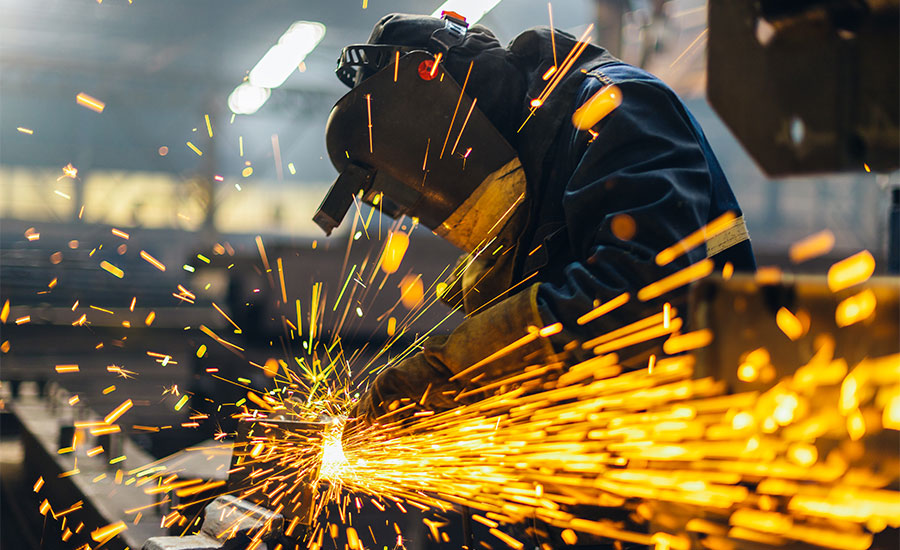
Understanding WPS standards is essential for designers, welders, and examiners included in welding operations. By adhering to WPS guidelines, welders can produce welds that fulfill the needed mechanical homes and structural stability. Inspectors count on WPS paperwork to verify that welding treatments are being followed appropriately and that the resulting welds are of excellent quality. Engineers make use of WPS requirements to design welding treatments that guarantee the durability and dependability of welded frameworks.
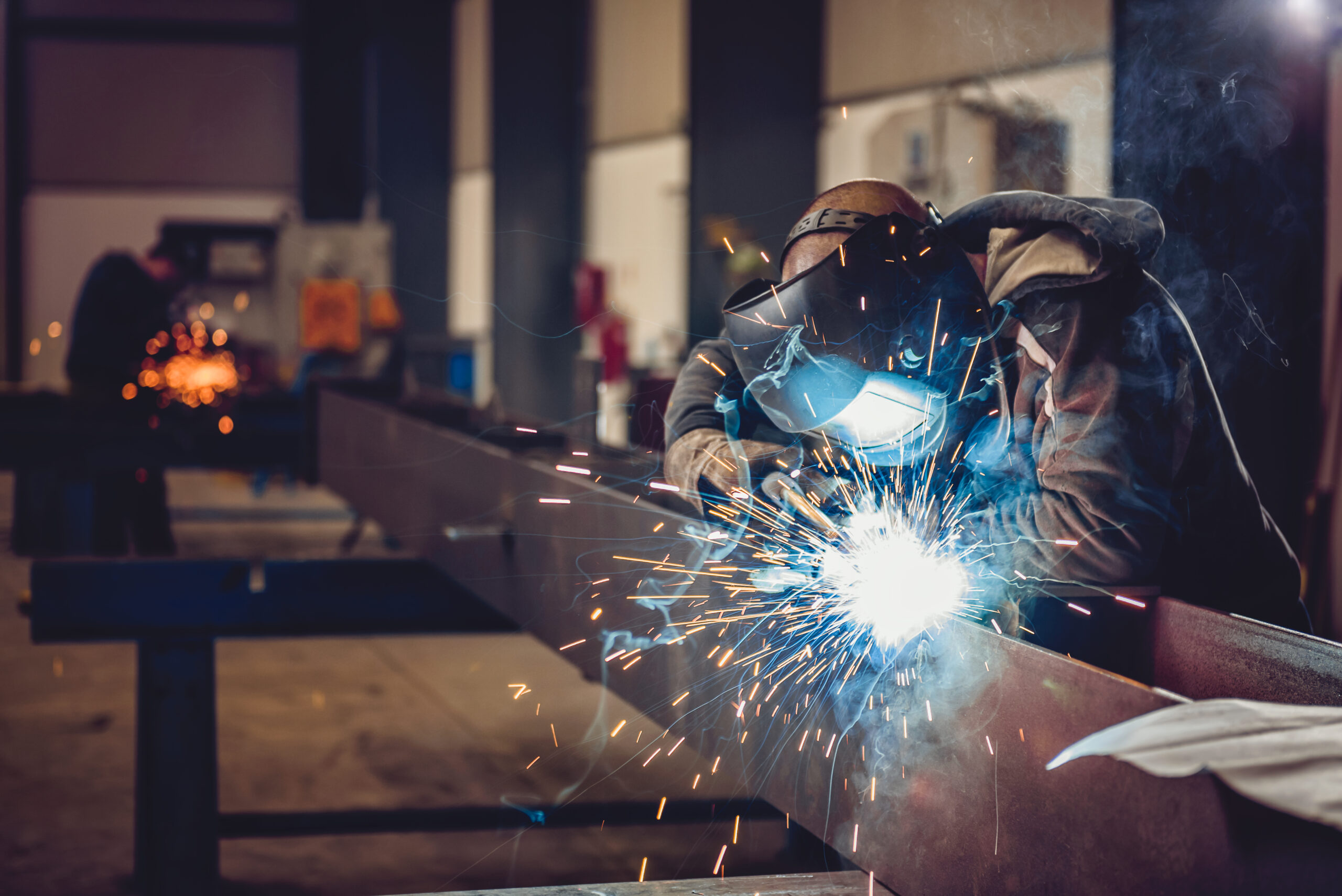

Necessary Devices for High Quality Welds
Understanding welding WPS standards is crucial for welders to successfully utilize the necessary tools needed for producing high quality welds. The type of welding maker required depends on the welding process being made use of, such as MIG, TIG, or stick welding. Wire brushes and damaging hammers are important for cleansing the weld joint before and after welding to eliminate any kind of impurities that might influence the quality of the weld.
Secret Strategies for Welding Success
To accomplish welding success, one have to master the crucial strategies important for generating top quality welds. One vital technique is preserving the right arc size. Keeping the electrode at the optimal distance from the workpiece is essential for creating strong, uniform welds. Additionally, controlling the travel speed is vital. Relocating too swiftly can result in inadequate infiltration, while relocating also slowly can result in extreme warm input and prospective problems. Proper control of the electrode angle is an additional essential technique. The angle at which the electrode is held can affect the bead shape and penetration of the weld. Moreover, making certain regular weapon angle and direction of travel is essential for uniformity in the weld bead. Finally, preserving a constant hand and a secure welding placement throughout the procedure is crucial to attaining accuracy and uniformity in the welds. By grasping these crucial strategies, welders can boost the top quality of their job and attain welding success.
Ensuring Conformity With WPS Specifications

Furthermore, welders should undergo training to familiarize themselves with the WPS standards relevant to their work. Regular audits and evaluations must be performed to confirm that welding activities align with the prescribed WPS guidelines. Additionally, maintaining detailed records of welding parameters, equipment calibration, and inspection outcomes is crucial for showing conformity with WPS criteria - welding WPS. By carefully sticking to WPS requirements, welders can guarantee that their work meets the needed top quality degrees and adds to the general success of the welding project.
Troubleshooting Common Welding Issues
When faced with common welding concerns, determining the root reason is vital for efficient troubleshooting. One prevalent trouble is Visit Website the visibility of porosity in welds, commonly triggered by impurities such as corrosion, oil, or wetness. To resolve this, guaranteeing correct cleansing of the base metal prior to welding and making use of the appropriate securing gas can substantially reduce porosity. An additional issue regularly experienced is absence of fusion, where the weld stops working to appropriately bond with the base material. This can come from poor warm input blog or inappropriate welding technique. Readjusting parameters such as voltage, cable feed rate, or travel rate can aid enhance blend. Additionally, distortion, cracking, and spatter are common welding challenges that can be minimized through appropriate joint prep work, consistent warmth control, and picking the suitable welding consumables. By completely comprehending these common welding concerns and their root causes, welders can properly troubleshoot issues and attain top quality welds.
Final Thought
In verdict, understanding welding WPS standards calls for an extensive understanding of the guidelines, utilizing important tools, and implementing crucial techniques for successful welds. Guaranteeing compliance with WPS standards is important for producing high quality welds and avoiding typical welding issues. By following best strategies and methods, welders can accomplish trustworthy and constant results in their welding projects.
In the world of welding, mastering Welding Treatment Requirements (WPS) requirements is a vital element that directly affects the high quality and stability of welds.When delving into the realm of welding techniques, a vital element to comprehend is the significance and complexities of Welding Treatment Requirements (WPS) criteria. WPS requirements offer a comprehensive standard for welding procedures, guaranteeing consistency, high quality, and safety and security in the welding process. The kind of welding maker needed depends on the welding procedure being utilized, such as MIG, TIG, or stick welding.Achieving welding success with the proficiency of key techniques basics requires a thorough understanding and adherence to Welding Treatment Specification (WPS) criteria.
Comments on “Welding WPS: Common Mistakes to Stay Clear Of and How to Correct Them”